PolyCharge Recognized by Semiconductor Review
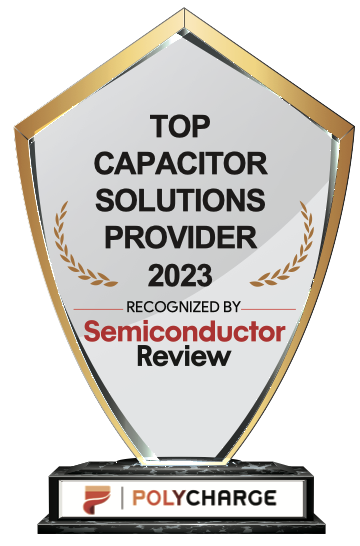
Using its proprietary—NanoLam™technology, PolyCharge is a manufacturer at the forefront in the development and production of advanced capacitor products ideally suited for next generation electrification applications. Smaller than conventional film and ceramic capacitors, PolyCharge capacitors can withstand higher temperatures making them ideal for high power applications.
Demand for PolyCharge products has increased dramatically because of these capabilities. Since its formation in 2018 the company has focused on highly customized designs with applications spanning several markets including automotive, aerospace, defense, medical, and industrial. Recently, however, PolyCharge announced that it will be releasing a new series of off-the-shelf products under its “ThermoLink™,” brand. ThermoLink™ capacitors, made with NanoLam™ Technology, are an easier way for OEMs and Suppliers to integrate PolyCharge products into their designs.
ThermoLink™ products will inherit all the benefits of PolyCharge’s NanoLam™ Technology. In addition to higher energy density and specific energy, ThermoLink products are self-healing and exhibit up to 3-times the thermal conductivity of conventional polypropylene capacitors. In most cases, due to the smaller size and unique form factor of ThermoLink™ capacitors, system level inductance is also lower resulting in greater efficiency. “OEM’s continue to seek smaller package sizes while simultaneously increasing power,” says Steven Yializis, Chief Operating Officer and Director of PolyCharge. Mr. Yializis continued, “The absence of alternatives to standard film and ceramic capacitors force the need for highly custom designs – where extraordinary expense goes into shaving a few milliliters and grams here and there. Of course, each new design requires testing and validation, which also adds to cost. ThermoLink™ products, on the other hand, can meet most volume and weight requirements without any customization.”
Initially, PolyCharge will be releasing ThermoLink™ products with a single package size with plans to expand the line in the future. ThermoLink™ capacitors are actively being sold to beta customers with a plan for a hard launch in Q1 of 2024. “Our plan is to have ThermoLink™ products meet AECQ200 certification requirements by in 2024,” added Mr. Yializis.
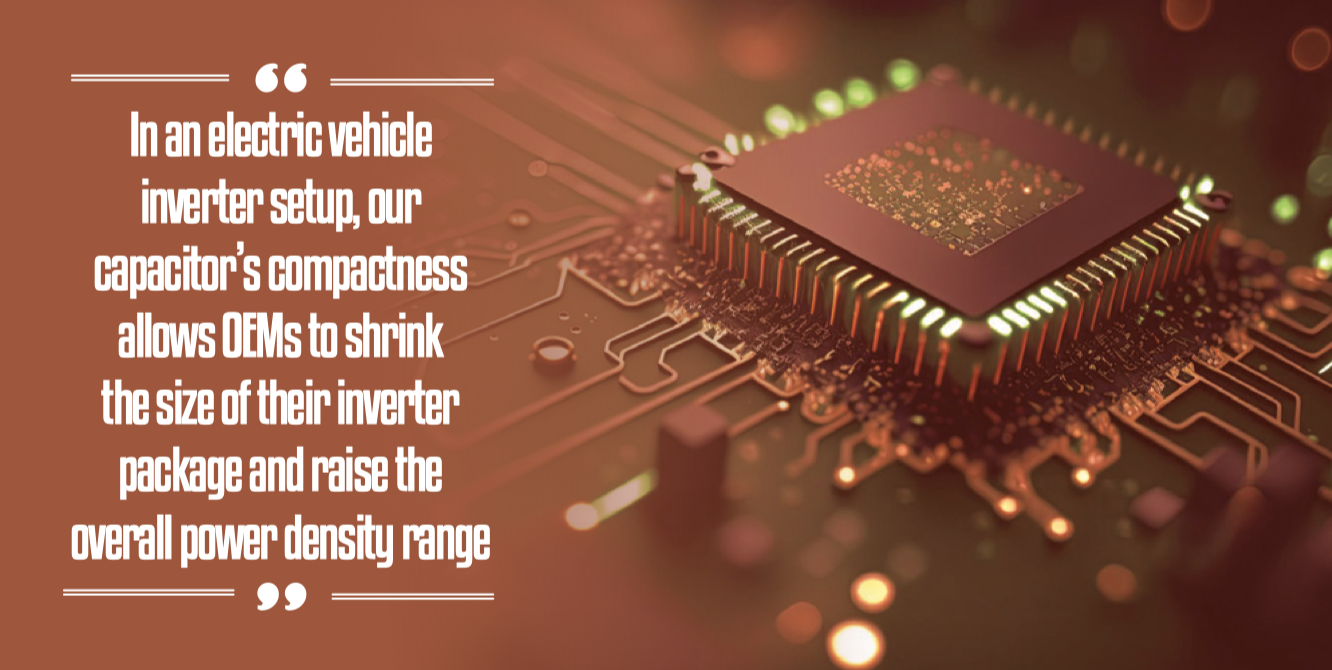
A spin-off from Sigma Technologies (www.sigmalabs.com), a former sister concern of General Electric, PolyCharge has a team of experts well versed in creating capacitors for high power applications using NanoLam™ technology as a foundation. Unlike most other film capacitors, NanoLam™ capacitors utilize thermoset resin systems to form the dielectric; this means, among other things, higher dielectric constant and higher temperature handling capabilities. Equally important is that PolyCharge’s decision to leverage thermoset resins eliminated the manufacturing constraints associated with thermoplastic resins. Specifically, unlike thermoplastic dielectric films, which are produced by melting, extruding, and stretching (or orienting) films on a completely separate line, which most capacitor manufacturers do not own, NanoLam™ capacitors are able to form the dielectric, the electrode, and the windings in the same machine. This allows NanoLam™ products to be cost competitive with more entrenched, conventional, technologies like film, ceramic, and hybrid electrolytic.
NanoLam™ is highly flexible from a design perspective as well. It can, using the same processes, meet the needs for applications requiring continuous high ripple current and low ESR while also meeting the needs for pulsed power application. A unique application of the NanoLam capacitor in the medical realm is within a power pack of a defibrillator. Since wearable cardioverter defibrillators (WCD) are carried in person, it is important to maintain a level of comfort and keep the capacitor as small as possible, which is otherwise the largest and heaviest component in a WCD. Using the same core technology to produce a DC link for automotive applications, the team at PolyCharge was able to produce a capacitor for WCD applications with a power density of 7.9 joules per cubic centimeter, which is virtually unheard of in the capacitor world.
PolyCharge, in a relatively short period of time, has established strong strategic partnerships with BorgWarner, Exxelia, Rheinmetall and many others. PolyCharge is working closely with BorgWarner to expand NanoLam™ supply capabilities in Asia where BorgWarner will produce NanoLam™ capacitors for its inverters, converters, and other systems. It has also teamed with Exxelia to produce NanoLam™ capacitors for aerospace and defense applications. Finally, PolyCharge has teamed with Rheinmetall to form Rheinmetall PolyCharge, GmbH to address production and supply needs on the European continent.
PolyCharge is committed to being the word leader in the development and production of high energy density, high temperature, capacitor products. In addition to its NanoLam™ technology PolyCharge is also working to develop a solid state supercapacitor with a dielectric constant measured in the “thousands,” and is seeking commercial partners to accelerate development. PolyCharge, in its surge to reinvent capacitor design, is continuously adapting to changes, and the focus is to move down the path of mass production on various designs from its partners in the automotive, aerospace, medical, and other industry sectors.